Mining
The control of metals in mining water is vital, be that in effluent facilities, in process applications, or on machinery maintenance issues. Site license agreements include specific treatment parameter that the AquaValid sensor can help maintain with the least amount of chemical consumption possible. And our Brine and Lithium alternatives can help optimize processes.
Where regulatory compliance is an issue, a real time log can provide proof of compliance.
Most common metals found in the Mining Industry
- Calcium
- Copper
- Cobalt
- Gold
- Lead
- Lithium
- Magnesium
- Manganese
- Zinc
Different Applications for the Sensor
Tailings Monitoring
Metals that escape through process can result in environmental fines and can risk site closures. Mining processes can cause quick variation in waters, meaning that Realtime monitoring is the only real solution to this issue. By catching these metals before they cause problems, facilities can save money through fines, overdosing of chemicals, and through man hours tied up in testing.
Machinery Maintenance
The metals running through your vital machinery have massive effects on the life of your machinery. Maintaining essential systems like boilers requires proper pre-processing. Knowing what is in the water before it reaches your systems and knowing the efficacy with which you are cleaning that water are essential tasks.
Process Optimization
Knowing the concentration and ratios of metals in fluids in real time is vitally important for process optimization. Extraction levels can vary significantly and have massive impacts on the revenue of the operation.
How the AquaValid Works
Aquavalid takes a small slip stream from the water flow, converts it to a plasma and records the spectral information from the plasma at about 5000C. At these temperatures most metal contaminants in the water start to glow. The raw data is reported to a cloud computing environment that analyzes the spectral information to determine the contaminants and quantity of each contaminant. The larger the quantity of a metal in the source water, the brighter that metal is in the generated light. This information can be reported to the SCADA systems controlling chemical injection to optimize the treatment. It is also stored and available as a report of graph of each contaminant, or groups of contaminants for regulatory reporting, historic analysis for planning purposed or other needs. Where multiple clients share a watershed the client may elect to share the information with clients downstream to provide advanced warning of changes in the source water.
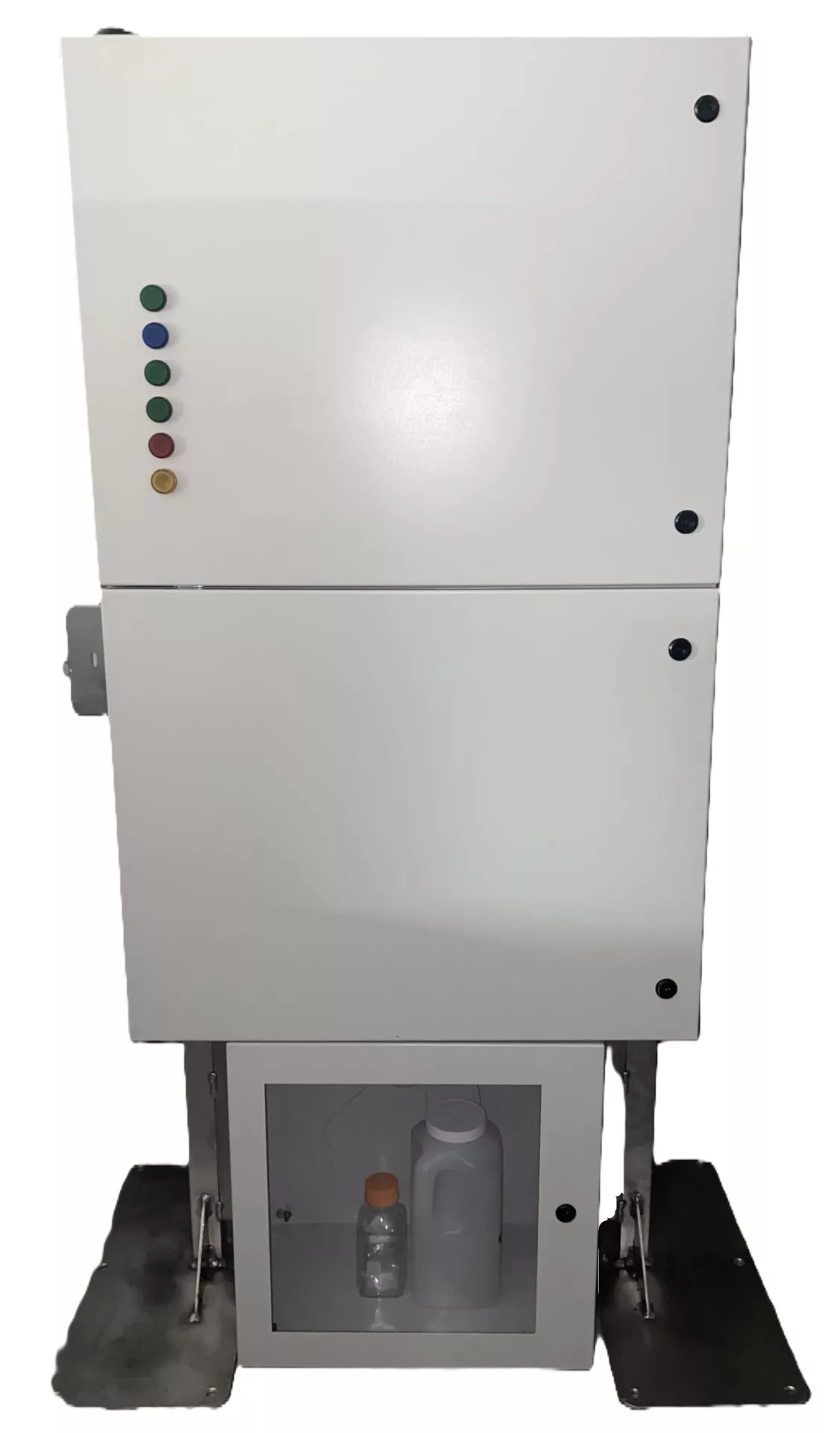